Micro Reactor
MicroReactors offer many advantages over
conventional scale reactors,
including vast improvements in
energy efficiency, reaction speed and yield, safety,
reliability, scalability,
on-site/on-demand production, and a
much finer degree of process control.
Using MicroReactors is somewhat different from using a glass
vessel.
These reactors may be a valuable tool in the hands of an
experienced chemist or reaction engineer.
Microreactor combines with micro mixing chip, micro heat
exchanger chip, micro flowing chip etc.
With its unique structure, it can quickly endothermic,
exothermic, heat up, mass transfer and others.
Depending on different reaction, it can divide into
liquid-liquid reaction,
gas-liquid reaction and gas-gas phases
reactions.
Using precision machining technology to
produce specific channels in 10 to 500 microns ID sizes,
with the common
characteristics of chemical reaction in a small space.
The average size of the channel is
generally micron or nanometer, and with tens of thousands
channels contained inside that can
achieve a very high yield.
The
Characteristic of MicroReactors:
1. Continuous reaction, time saving, small footprint
2. High precise controllability, surface area, fast heat and
mass transfer efficiency
3. Safe and reliable, sealed, small moment holdings
4. Less byproducts, reduce pollution, low environmental costs
5. No amplification effect, reducing the pilot variations,
shorten development cycle
6. Wide operating range, suitable for a variety of reactions
7. Intergated device, quick installation
8. Stable quality
Leading with Quality, Performance and Cost
Our partners, the FRAPP'S Chemical
Industrial is a high-tech enterprise that focuses on research
and
production of the Pneumatic Driving Pressure Filter with
independent intellectual properties,
that based on the
integration and refining of the global research and engineering
practice.
Our main equipments is for mixing, reacting, synthesizing,
extracting process in the chemical production
technologies, in
the fields like phosphorus chemical industry, petroleum chemical
industry,
fine chemicals and so on.
We also have advanced technology on dust-free cooling equipment
of solid particles, powder materials.
www.frappsbio.com
Product R&D
process comparison
|
Microchannel
Reactor |
Conventional
Reactor |
Application span |
Specific
reaction |
Generic
application |
Continuity |
Continuous |
Batch |
Heat transfer efficiency |
High |
Low |
Control and condition |
Precise |
Difficult |
Efficiency |
High |
Low |
Materialv distribution |
Uniform |
Non-uniform |
Byproduct |
Low |
High |
Security |
High |
Low |
Initial Cost |
High |
Low |
The main materials of
Microchannel Reactor are Titanium, Zirconium alloys and
Hastelloy.
The three-dimensional structure element for carrying
out the chemical reactions is based on
solid matrix and produced
by special micro-processed technology, that can largely increase
the surface
contact probability, and enable adequate reaction of the
raw materials.
Suitable reactions:
Sulfonation, Methylation,
Hydrogenation, Nitration, Oxidation, Esterification,
Diazotization reactions.
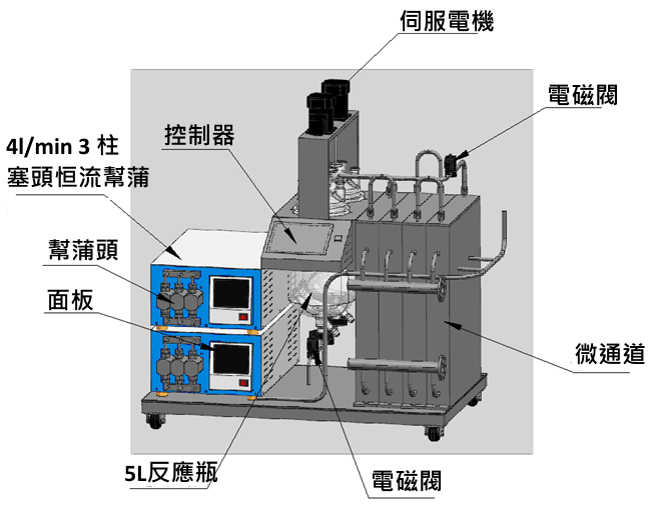
Schematic diagram: Fixed bed
debenzylation
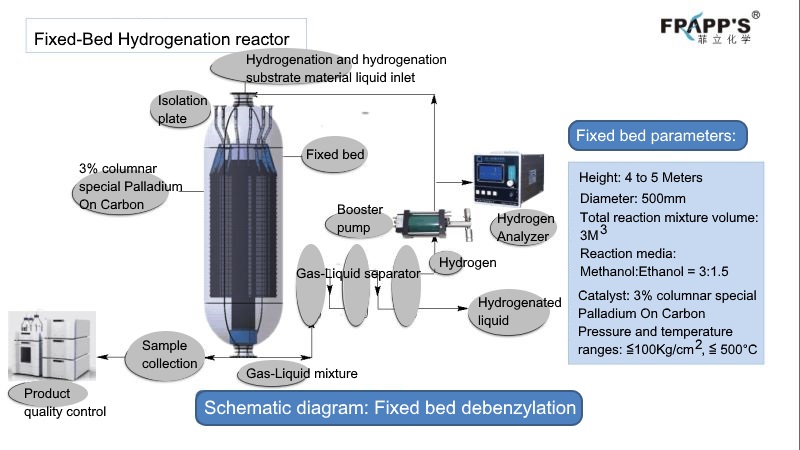
Diazomethane
Applications
Click to enlarge
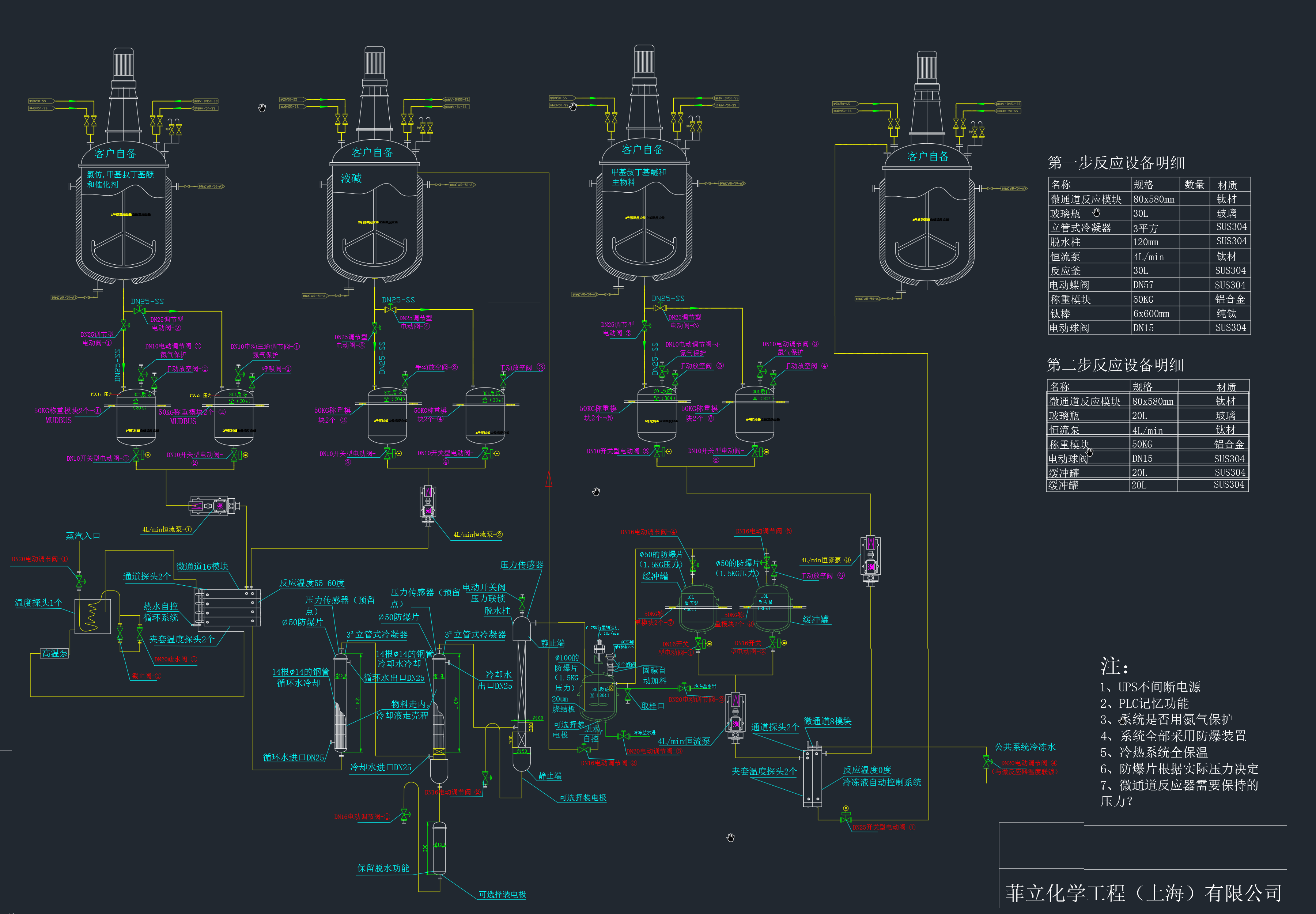
Procedure example:
1. Add Chloroform, methyl tert-butyl ether and catalyst
into 3000L, No.1, premix reactor, stirring until clear, and prepare for use.
2. Put Caustic soda into 3000L No.2 premix reactor , and prepare for use.
3. Methyl tert-butyl ether and the main material was dissolved in 3000L, No.3
premix reactor, and prepare for use.
4. Using two sets of 30L No.1 and No.2 stainless steel Material Preparation
reactors that are equipped with weighing modules, first put 25KG material into
the No.1 Material Preparation reactor, then after completion, immediately switch
to No. 2 Material Preparation reactor for reparation, and start the isocratic
pumps, conduct material form No.1 Material Preparation reactor into the
microchannel, after completion of the feed when the scale of weighing module is
lower than 50 to 80 grams,it will automatically switche to the No.2 Material
Preparation reactor and proceed in sequential loop. On the outlet of No.1 and
No.2 Material Preparation reactors,there are DN10 electric switch valves
equipped for system nitrogen protections。
5. Using two sets of 30L No.3 and No.4 stainless steel Material Preparation
reactors that are equipped with weighing modules, first put 25KG material into
the No.3 Material Preparation reactor, then after completion, immediately switch
to No. 4 Material Preparation reactor for reparation, and start the isocratic
pumps, Conduct material form No.3 Material Preparation reactor into the
microchannel, after completion of the feed when the scale of weighing module is
lower than 50 to 80 grams,it will automatically switche to the No.4 Material
Preparation reactor and proceed in sequential loop. On the outlet of No.3 and
No.4 Material Preparation reactors,there are DN10 electric switch valves
equipped for system nitrogen protections。
6. The microchannel reactor temperature was set at about 70 ℃, the reaction
temperature is controlled at 55-60 ℃.
7. Reacted material is cooled through water(a 3 square vertical tube condenser)
and refrigeration brine(a 3 square vertical tube condenser), and then dehydrated
with electric control valve equipped at the bottom to automatically discharge
water.
8. Using a 30L small reactor equipped with a sintered plate and stirrer, add
into 10KG sodium hydroxide, conduct the dehydrated reaction liquid from into the
bottom to dehydrate with sodium hydroxide again, and then go out from bottom
flange of the reactor. At the outlet, there is equipped with a 6*300 Titanium
rod filter to prevent from flowing out of sodium hydroxide together with the
material. Two DN57 electric butterfly valve is equipped in serial at the top of
the reactor for adding sodium hydroxide. Sodium hydroxide is put between the
valves when the upper electric valve is opened, and then the upper electric
valve is closed before the openning of the lower electric valve, ,thus
preventing the diazomethane gas from leakage.
9. The dehydrated reaction liquid is conducted into a 10L buffer tank, and ,
when the filled material reaches top limit point, start 3# isocratic pump, and
in the same time, start 4# isocratic pump to pump materials form #3 Material
Preparation reactor into the microchannel for reaction, with microchannel
reactor temperature at 0 ℃. The reacted material flows back to the reactor for
further processing.
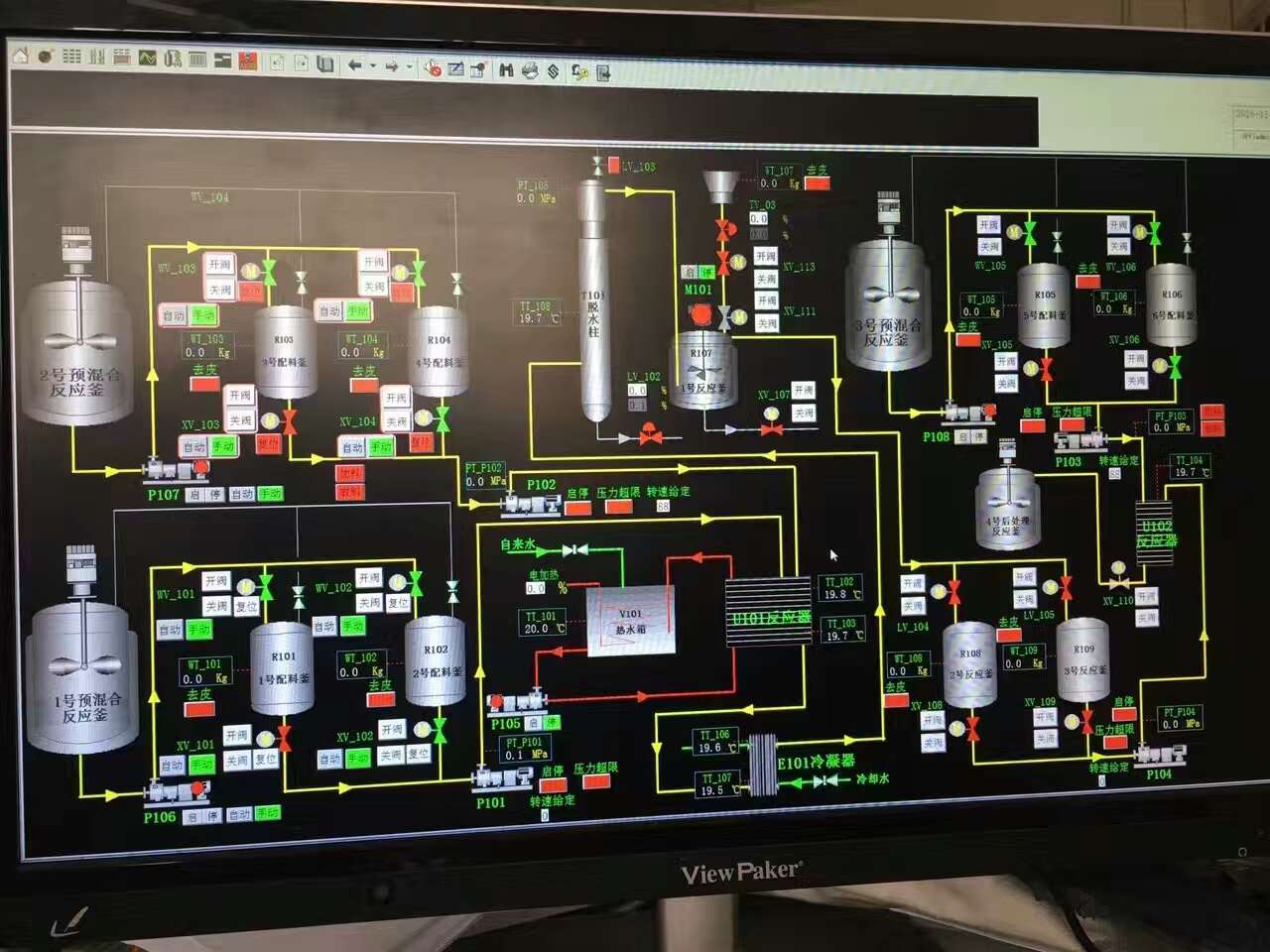
|